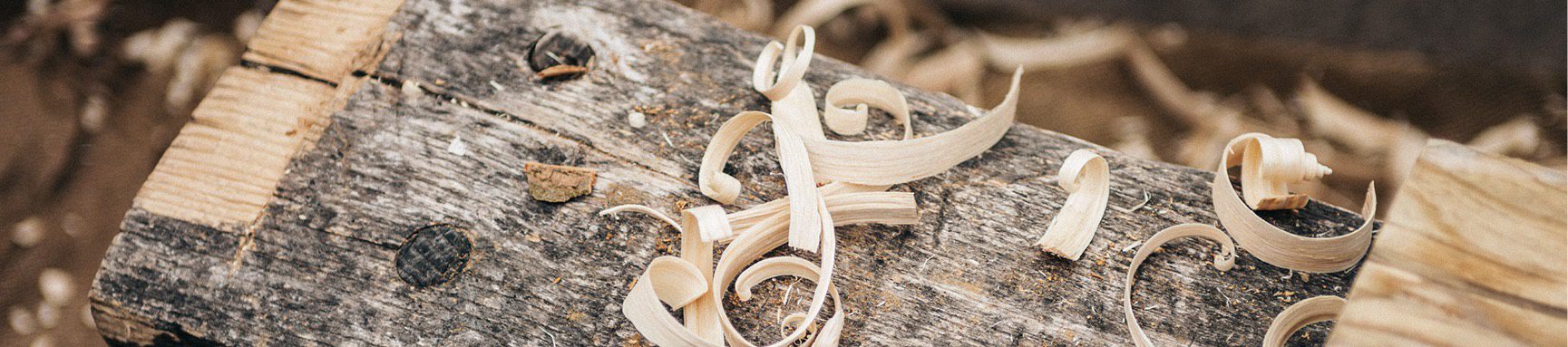
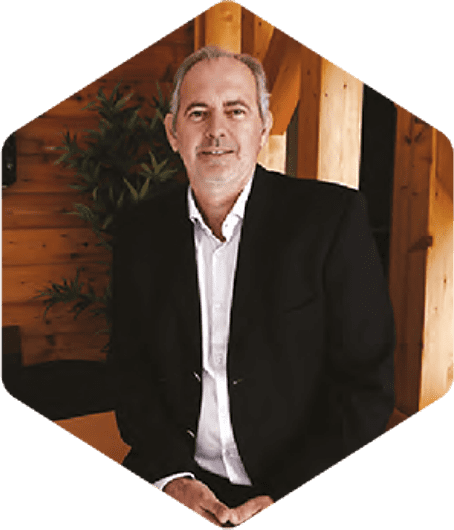
Foundation of
Deco Charpente and
development of
the company from 4 to 20
employees between 2007 and
2016
2012
Acquisition of a
new Center
machining
(size machine)
2017
Déco Charpente matters
now 10 points of sale.
Objective: Opening
3 to 5 points of sale/year

2007
Implementation of the workshop
link manufacturing to
Brignoles of 1000 m²
Creation of a Service
Commercial and a
Integrated design office
at the workshop
2013
Deco Charpente for-
follows the development
of his network.
Objective: Opening
3 points of sale/year
2023
Trusted suppliers
supported by
New industrial and digital production tool
Goals : modernization, digitalization and improvement of the company's production tools to guarantee its sustainability.
“Project co-financed by React EU – European Union recovery system in response to the Covid-19 pandemic”
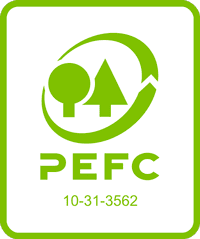
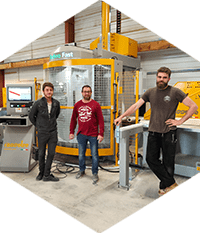

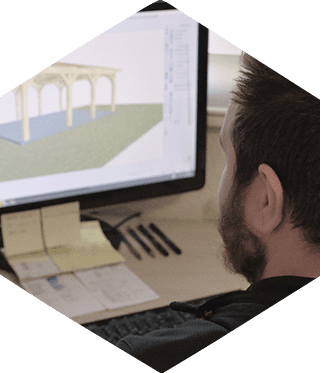
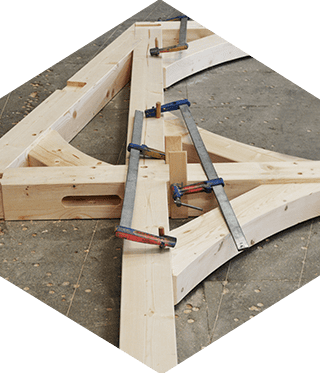
As part of an order, after fine-tuning and precise measurements from customers, the design office produces 3D plans down to the smallest detail in order to validate the project before manufacturing. This first step is essential, it is a real referee, it brings everyone into agreement.
Once validated, the plans are transferred from the design office to the numerically controlled machine. The carpenter, who controls the machine, machines each piece of wood, each of them is identified, then transported to the processing area. This second stage, called wood cutting, is the exact reflection of the 3D plans.
In the design area, two other carpenters carry out a blank assembly of all the pieces of wood in order to check the entire shelter in its smallest details (assembly, cuts, slope, etc.). This third step represents internal quality control, it is the assurance of maximum satisfaction for all customers. Once the manufacturing of the shelter is completed, Déco Charpente stores it in its workshop while awaiting installation.